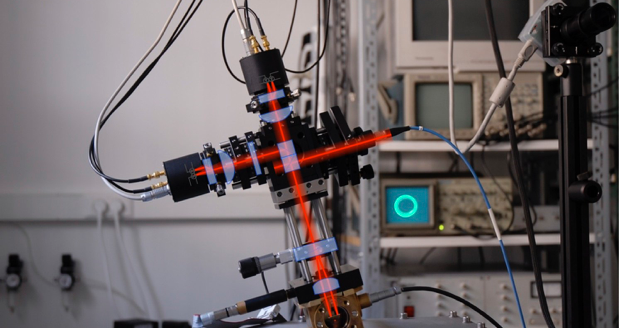
The nanometer target
For decades, miniaturization has led to ever more integrated and energy efficient devices, challenging micro-electronics and mechanics industries. A major issue to overcome nowadays is the lack of characterization and manipulation tools at the nanometer scale. On the academic side, many fundamental questions of quantum mechanics and statistical physics are still open at such small scales, like the description of mesoscopic interactions or the role of fluctuations. The conception and realization in our laboratory of an AFM (Atomic Force Microscope) with high resolution in force led to an original instrument to tackle these fundamental questions and their applications, with a world leading precision. Indeed, using a quadrature phase differential interferometer, we can measure the deflexion of the force sensor (micro-cantilever) with a 1 fm/rtHz resolution in a several μm input range, a 10 to a 100 fold improvement of both sensitivity and range with respect to commercial systems. Though imaging capability is equivalent, our resolution in force spectroscopy (force dependance on tip-sample distance) is much sharper.
Nanoscale peeling
We study for example the mechanical response of a carbon nanotube pushed perpendicularly against a surface. The nanotube is grown directly at the AFM tip apex in collaboration with groups in Grenoble, Bordeaux or Lyon. Its diameter to length ratio makes it highly flexible, and its buckling leads to nN forces, usually hard to tackle. A strong signature can be read on force-compression curves: the interaction is attractive, with long force plateaux during retraction. A simple model of nanoscale peeling accounts for this behavior: the work done by the force F to peel a length dl from the substrate is Fdl, and releases an energy Eadl, where Ea is the interaction energy per unit length of the nanotube with the substrate. Energy balance in a quasi-static peeling thus leads to F=Ea, the force plateau. This experimental observation not only hints at the physical process, but also gives a quantitative measurement of the adhesion energy. Such information paves the way for an optimization of the coupling of nanotubes with their environment in applications.
Thermal noise as a tool
Far from being just a limitation, thermal noise is used in our setup to probe the mechanics of the nanotube-substrate contact. Indeed, these natural fluctuations of the micro-oscillator {AFM cantilever + nanotube in contact} are used to measure the resonant frequency shift with a time-frequency analysis. Without requiring heavy experimental facilities such as electron microscopy, this innovative tool characterizes in situ the flexibility of the nanotube, thus its intrinsic properties, in addition to its external interactions.
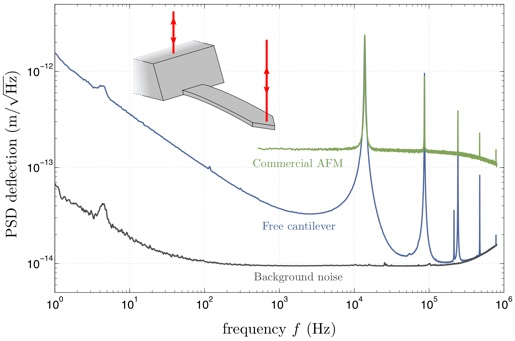
At room temperature, thermal noise excites the normal modes of a free AFM cantilever. The background noise of our interferometric measurement is intrinsically 10 times smaller than that of commercial systems, leading to much shaper resolution on the power spectrum density of fluctuations of the deflexion.